Cladding Sheets and the Right Cover Material – Protection and Durability for All Conditions
Cladding sheets and their application are an essential part of industrial and technical insulation projects, providing both mechanical protection and long-term durability in various environmental conditions. The choice of appropriate cover material determines the efficiency of insulation, protecting it from weather, corrosion, and mechanical damage.
What Are Cladding Sheets and Why Are They Important?
The usability of industrial insulation for different purposes and conditions depends not only on the insulating properties of the materials but also on the choice of appropriate cover materials. In many industries, such as paper, chemical, food, and energy sectors, equipment is often used in humid and chemically active environments.
Many pipelines, equipment, and tanks are located outdoors, where they are exposed to all environmental impacts. Even indoor environments can experience significant temperature fluctuations, sometimes posing greater challenges than outdoor conditions. All these factors, along with many others, influence the properties and lifespan of insulation.
In addition, the mechanical properties of the insulation cover are often critical, such as resistance to compression, tension, bending, vibration, impacts, and hardness.
Due to these factors, selecting the right cover material is essential.
Metal Sheet – The Most Common Cover Material for Industrial Technical Insulation
Today, metal sheet is the most commonly used cover material for industrial technical insulation. Smooth sheet metal is generally used for covering pipelines, equipment, and smaller tanks, while profile sheet metal is primarily used on flat surfaces, such as large tanks, boilers, and industrial electrostatic precipitators. Exceptions include the use of fire-resistant fabrics, foils, plastic materials, and others as cover materials.
Cladding Sheets Are Designed To:
- Protect insulation from mechanical damage.
- Shield insulation from weather-related effects, such as:
- Corrosion caused by moisture.
- Brittle degradation of insulation due to UV radiation.
- Erosion of surface layers caused by airborne particles in windy conditions.
- Protect insulation from industrial corrosive environments.
- Facilitate easier cleaning of insulation, maintaining high hygiene standards (e.g., in the food industry).
- Prevent dust generation from insulation materials.
- Enhance the appearance of insulation and integrate it with architectural designs.
Considerations When Choosing Cover Materials
When selecting cover materials, it is crucial to consider their properties and applicability in different environments based on specified conditions. It is also important to remember that the support structures and fastening elements of insulation cover materials play a significant role in the overall integrity of the insulation.
Examples of Key Considerations:
- Heat bridges, solar radiation, and other heat sources can significantly increase the surface temperature of cladding sheets.
- In the event of a fire, cladding sheet temperatures can rise drastically. For this reason, the use of aluminum cladding sheets in high fire-risk areas should be avoided.
Main Types of Cladding Sheets and Cover Material Benefits
Depending on the application and purpose, cladding sheets are made from various materials. The most common materials are:
1. Galvanized Steel Sheet (Operating Temperature: 200°C / –60°C)
Galvanized steel sheets are used in situations where surface coatings do not require special demands. With a zinc layer thickness of 275 g/m² or 350 g/m², the material offers high strength, hardness, significant corrosion resistance, and low cost. The melting point of zinc is 420°C. At high temperatures (around 900°C), the zinc layer ignites and burns with a bright flame, releasing toxic zinc oxide, which can cause poisoning if inhaled.
Zinc salts, formed when zinc comes into contact with acids (even weak ones like those in food such as oxalates, rhubarb, apples, etc.), are highly toxic. Therefore, galvanized steel should not be used in the food industry. The lifespan of galvanized steel depends on the wear of the zinc layer, which averages 0.6–1.2 micrometers per year depending on the environment, resulting in a lifespan of 20–40 years. In coastal areas and pools, wear rates increase to 2.1–4.2 micrometers per year.
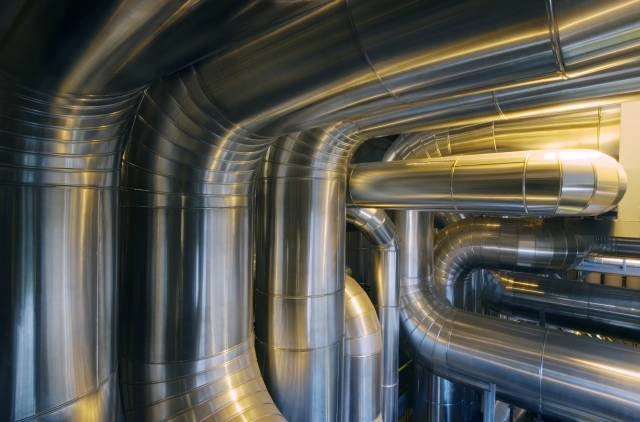
2. Stainless and Acid-Resistant Steel (Operating Temperature: 800°C / –200°C)
Stainless steel (RST; AISI 304) and acid-resistant steel (HST; AISI 316) cladding materials are used in harsh environments where galvanizing is no longer sufficient for corrosion prevention. Key applications include the chemical, paper, and food industries, as well as environments with heightened hygiene requirements, such as the medical industry.
Stainless steel is a 20th-century invention—a metal alloy consisting of iron as the main element, with chromium and nickel added to prevent corrosion. To qualify as “stainless steel,” the alloy must contain over 12% chromium, which forms a thin protective oxide layer. Higher chromium content improves corrosion resistance, while nickel enhances overall durability, especially in chloride-rich environments.
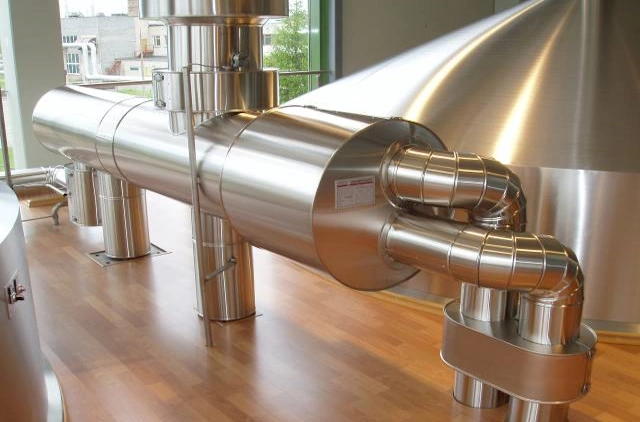
3. Aluminum Sheet (Operating Temperature: 300°C / –60°C)
Aluminum offers excellent properties such as good corrosion resistance and low density, making it highly useful as a cladding material. Its surface forms a thin, dense oxide layer that protects against further corrosion.
Advantages over galvanized steel:
- Better resistance to acidic environments.
- Does not produce sparks under friction or impact.
- Weighs only a third of galvanized steel.
- More aesthetically pleasing appearance
Disadvantages:
- Unsuitable for fire-resistant insulation (melting point: 620°C).
- Requires more careful handling during manufacturing.
- Mechanically weaker and more prone to damage than steel.
- To achieve similar strength, thicker sheets are needed, increasing cost.
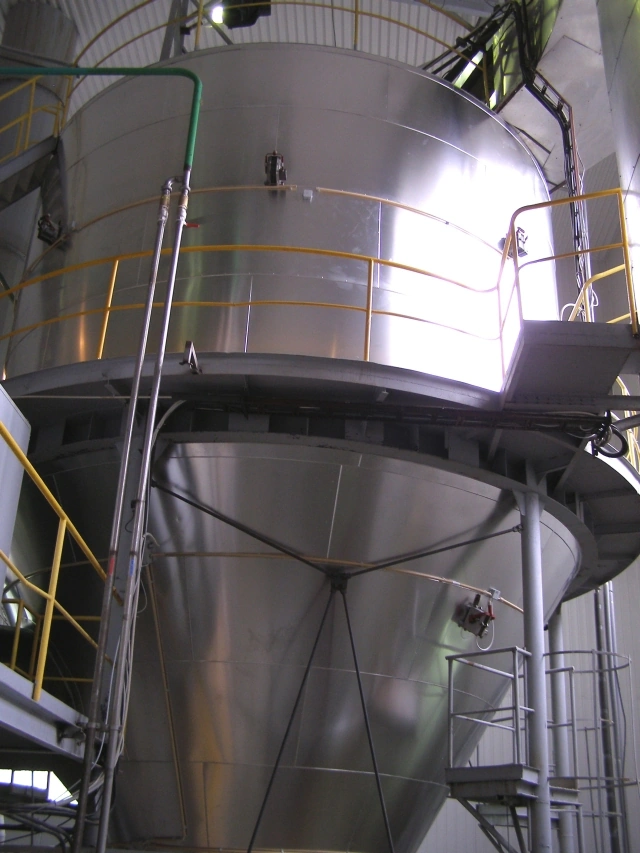
4. PVC-Coated Galvanized Steel (Operating Temperature: 100°C / –60°C)
This material features a polyvinyl chloride-based coating, offering excellent workability and high corrosion resistance, even in harsh industrial and coastal conditions. However, it does not withstand UV radiation well.
5. PVDF-Coated Galvanized Steel (Operating Temperature: 110°C / –50°C)
Polyvinylidene fluoride (PVDF) coatings are known for their exceptional color retention, making them ideal for applications where long-lasting color is critical. The downside is their susceptibility to scratches.
6. Painted Galvanized Steel (Operating Temperature: 100°C / –60°C)
Painted steel sheets are made from pre-galvanized and painted steel, suitable for use in indoor environments with low humidity and light environmental impact, such as clean air conditions.
Common paint types include:
- Polyester: Provides good resistance to weather, corrosion, and abrasion.
- Pural: A polyurethane-based coating that withstands UV radiation well and remains flexible even at low temperatures, with excellent chemical stability.
Other metals, such as copper, tin, and Aluzinc, are occasionally used as surface coatings for steel sheets.
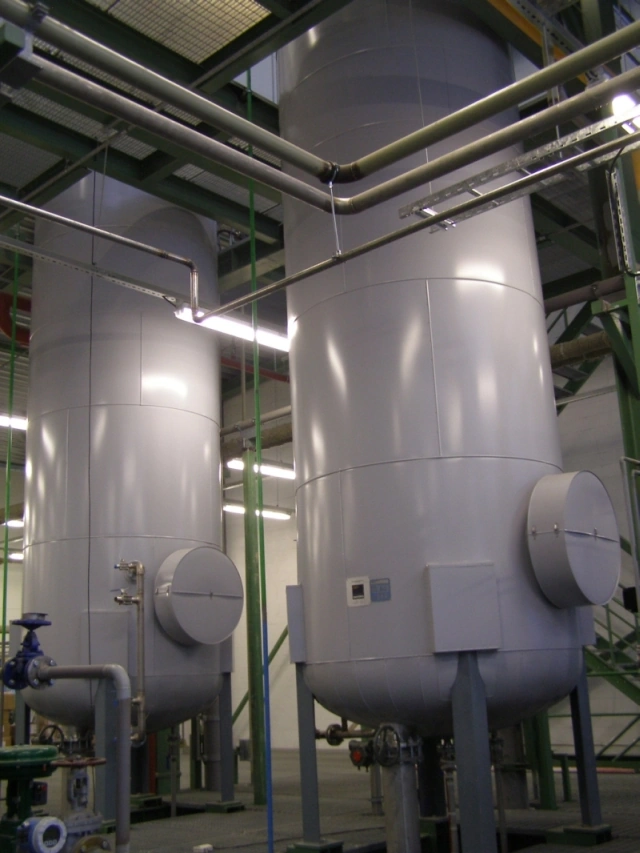
Looking for Professional Cladding Sheets and Insulation Solutions?
Contact us, and we will create a solution tailored to your needs, ensuring long-term reliability and protection! Contact Us.